APS Platform MES
Innovative solution for supporting production execution processes
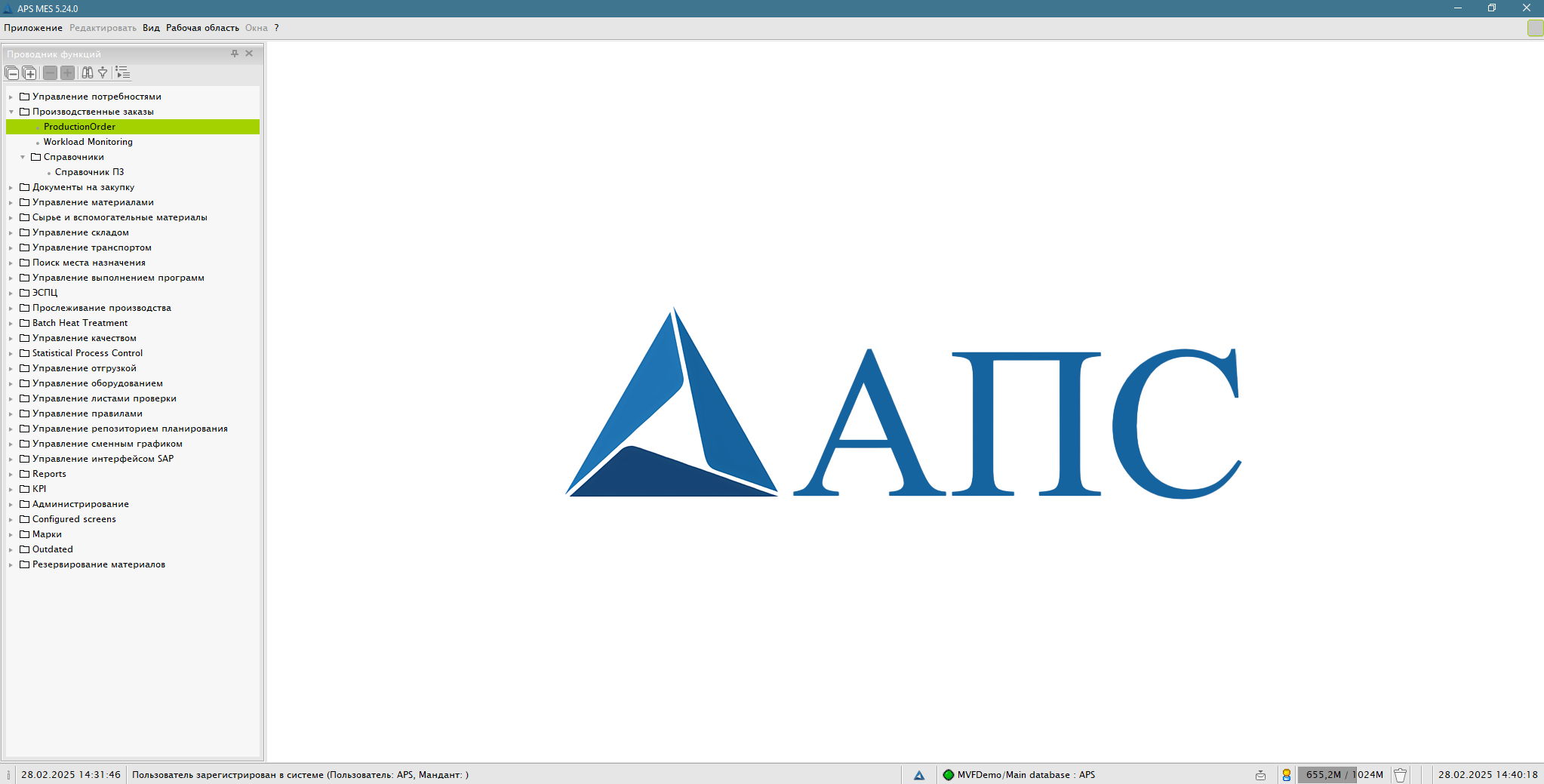
What is MES?
MES represents a comprehensive solution supporting all production processes of a metallurgical enterprise, enabling quick results and benefits from implementation.
This is achieved:
- A unified approach for processing, storing, and analyzing data obtained during production
- Complex calculations based on operational data and master data
- Minimizing adaptation costs for continuous process improvement
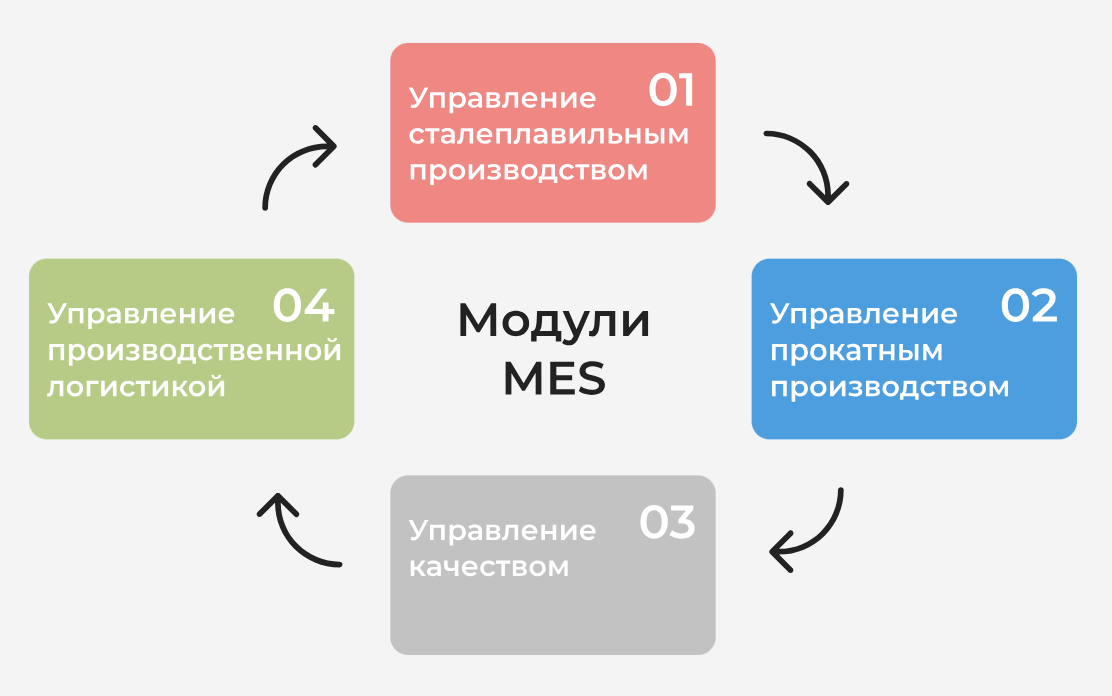
MES Modules
APS Platform MES includes the following modules
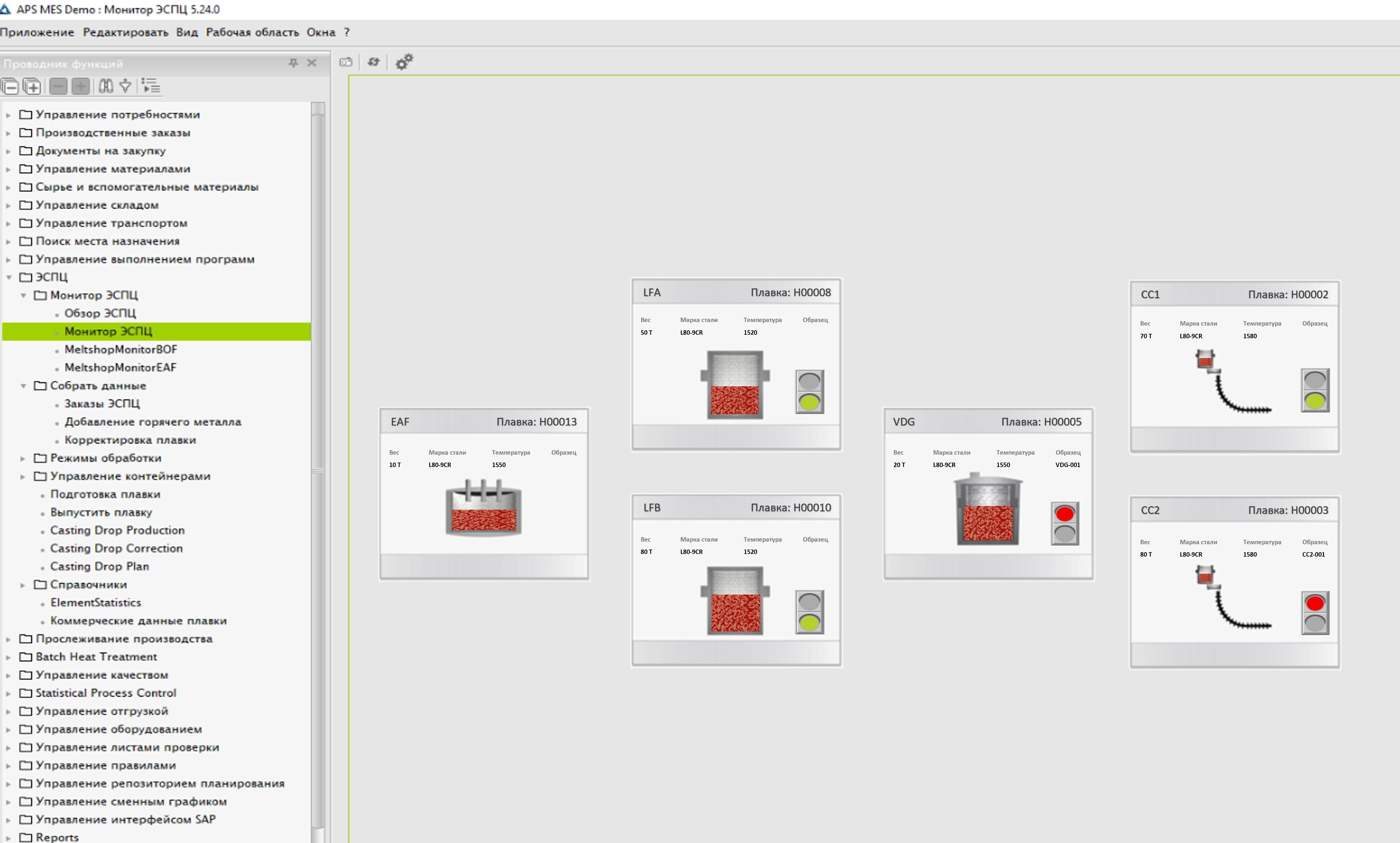
Key Benefits
Submodules
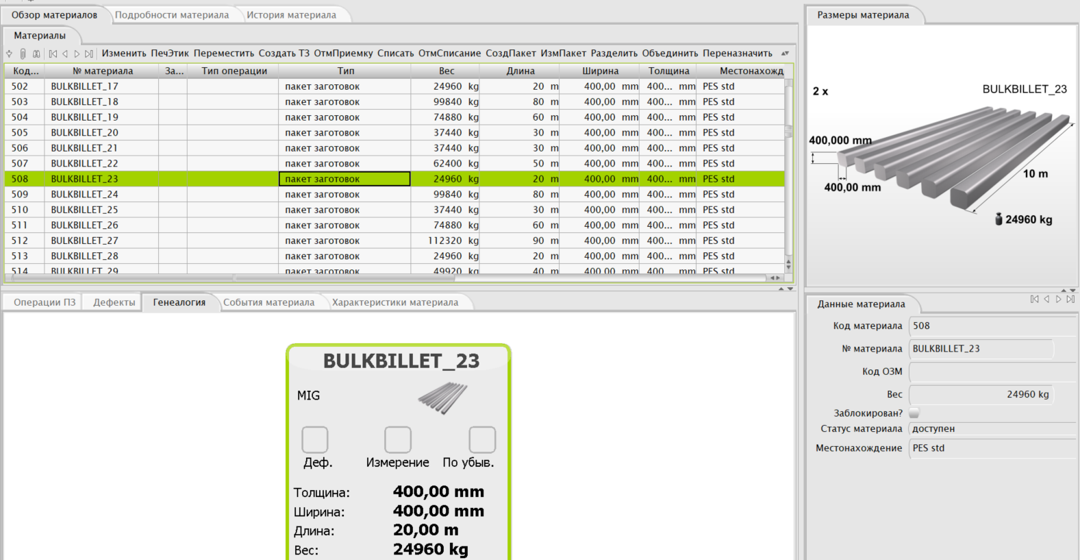
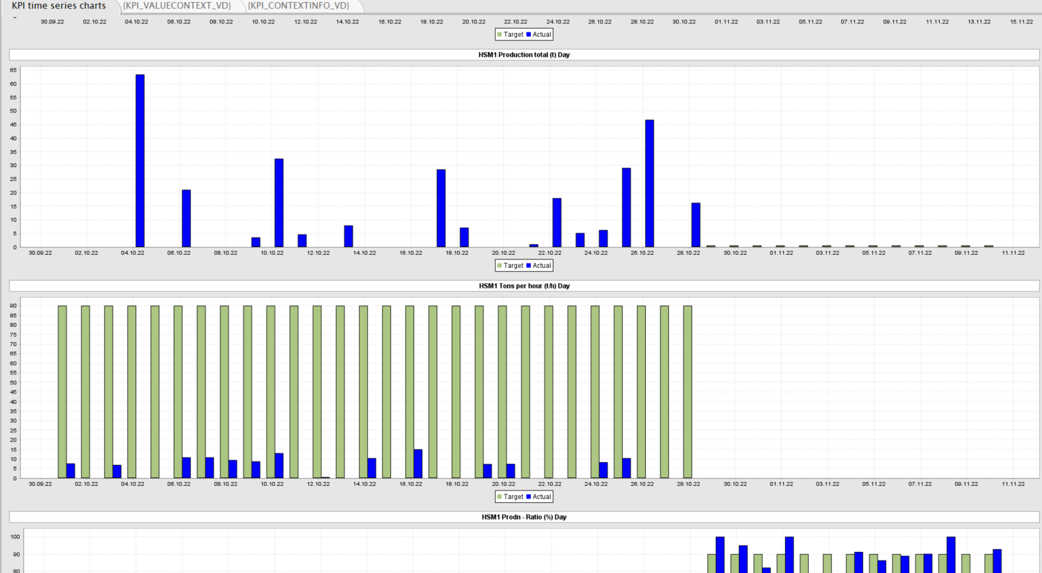
Main Functions
Main Principles
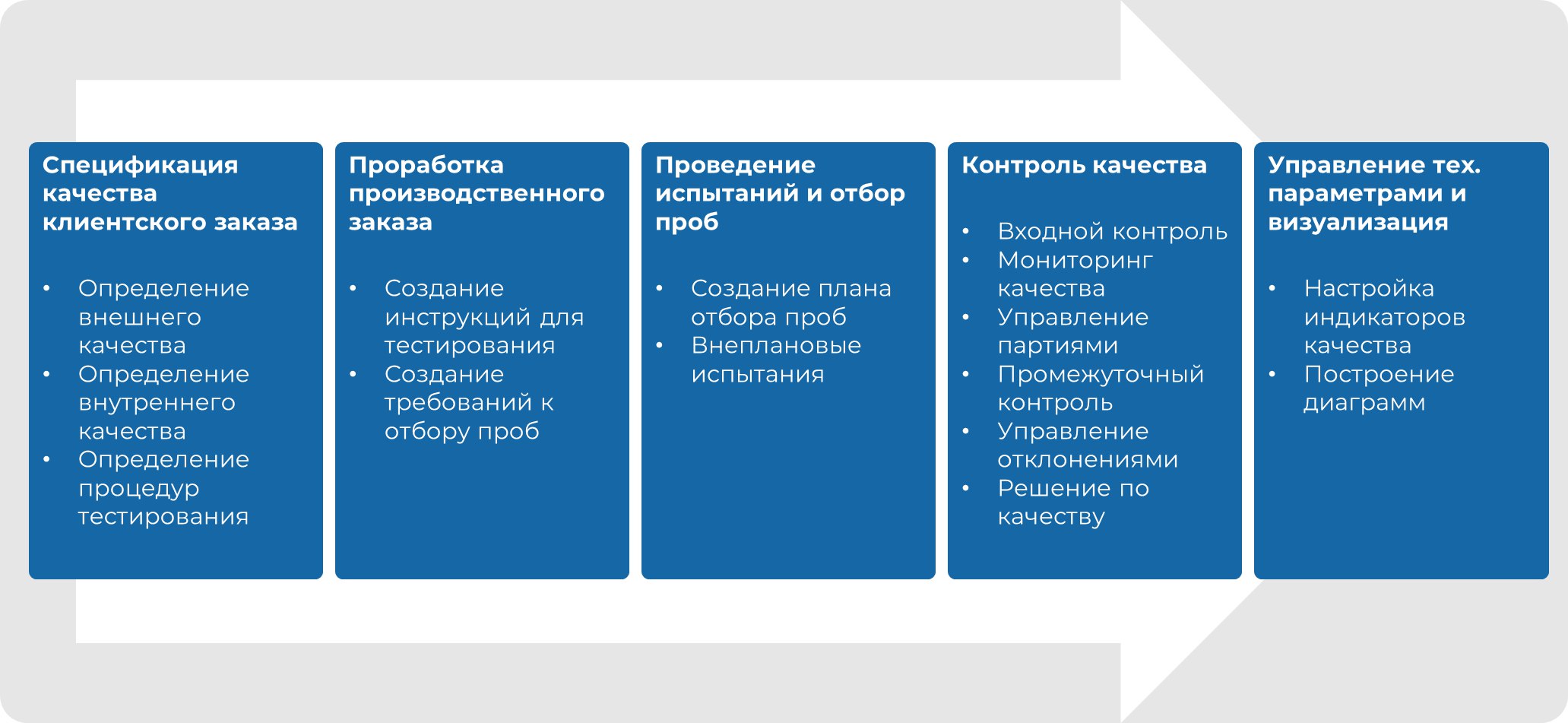
Key Benefits
Key Benefits
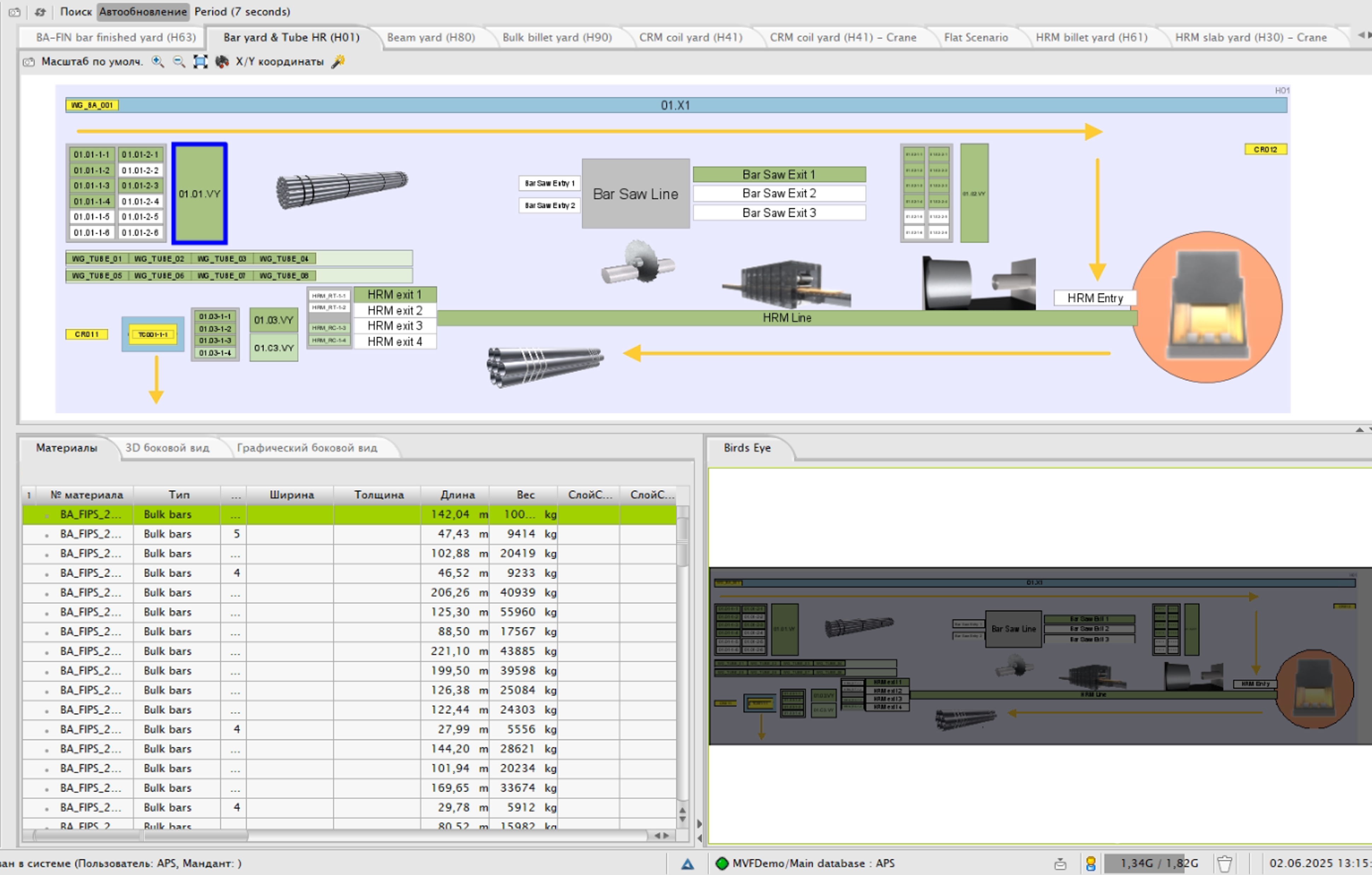